Zadanie
W poniższym artykule przedstawione zostało studium przypadku doboru sprzętu i algorytmu służącego do automatycznej inspekcji wizyjnej oznaczeń na metalowej, błyszczącej powierzchni. Inspekcja dotyczy wykrycia wielokrotnego napisu na metalowej obręczy lub braku napisu.
Problem
Stworzenie skutecznego systemu kontrolnego, wykonującego automatyczną inspekcję produktów, to złożone zadanie. Mimo różnorodności dostępnych na rynku komponentów i rozwiązań, opracowanie takich systemów wymaga starannego doboru i parametryzacji wszystkich jego elementów sprzętowych oraz programowalnych.
Szczególnie trudne do inspekcji są produkty odbijające światło, np. metalowe lub posiadające metalową powierzchnię. Inspekcja wspomnianych powierzchni jest trudna, ponieważ wymaga doboru odpowiedniego oświetlenia w celu całkowitej eliminacji odblasków na metalu.
W niniejszym artykule opisana jest automatyczna inspekcja wizyjna, której zadaniem jest wykrycie zdublowanych napisów na metalowym elemencie w kształcie okręgu o średnicy zewnętrznej 260 mm. Poddawany inspekcji wizyjnej napis ma wysokość ok. 5 mm.
Zadaniem systemu wizyjnego jest automatyczne wykrycie:
- Braku napisu
- Wykrycie sekwencji napisów większej niż jeden.
Na zdjęciach inspekcji znaki firmowe produktu zostały zamazane.
Stanowisko inspekcji wizyjnej
W pierwszej fazie projektu, firma zainteresowana automatyczną inspekcją wizyjną, w celu rozpoznawania napisów na metalowej obręczy, chciała stworzyć stanowisko ze stołem obrotowym, które obracałoby element metalowy o 360°. Wg. firmy, obrót umożliwiłby odczytanie oznaczeń znajdujących się na poszczególnych fragmentach obręczy (obserwowanych z punktu widzenia kamery).
Rozwiązanie to, wymagałoby wymiany obecnego transportera z jednoczesnym dołożeniem do stanowiska stołu obrotowego, który obracałby metalową obręczą o zadany kąt. Jest to rozwiązanie, które niewątpliwie generuje dodatkowe koszty do automatycznego systemu inspekcyjnego.
Dodatkowo, w rozwiązaniu sugerowanym przez firmę produkującą metalową obręcz, detal nie byłby widziany przez kamerę w całości i nie dało by się poprawnie stwierdzić, czy badane oznaczenie jest widziane w całości. Co za tym idzie, inspekcja byłaby niepoprawna.
Powyższe założenia inspekcji nie są optymalne do detekcji znacznika na metalowej obręczy i z tego względu inżynierowie z CUBE SYSTEMS sugerują umieszczenie systemu wizyjnego nad transporterem, na którym poruszają się metalowe obręcze – sugerują system wizyjny, który działałby bez wymiany obecnego stanowiska.
W zaproponowanej koncepcji, elementy są widziane w całości z użyciem wyłącznie jednej kamery o dużej rozdzielczości. Dzięki temu, obiekt poddawany inspekcji, jest widoczny w całości. Zmiana transportera i dokładanie do niego dodatkowych elementów automatyki nie jest wymagane.
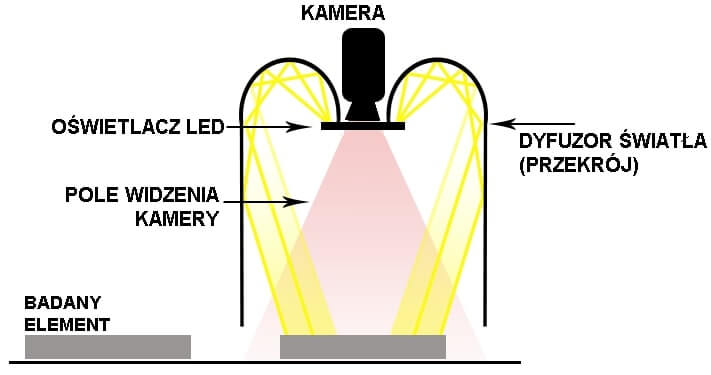
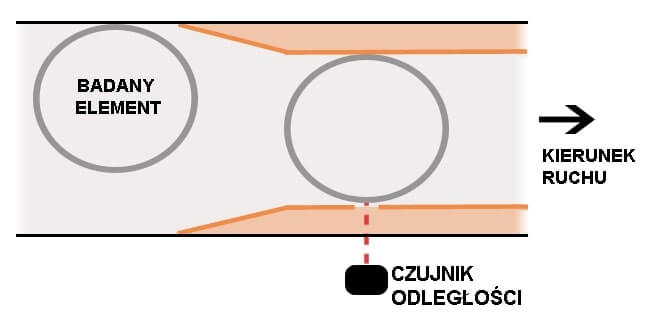
Wizualizację proponowanego stanowiska do automatycznej inspekcji wizyjnej oznaczeń na metalowym elemencie w kształcie okręgu przedstawiono na Rys. 1 oraz 2.
W pierwszej kolejności należy ustawić badany obiekt w całości w polu widzenia kamery - metalową obręcz na transporterze należy odpowiednio spozycjonować w stosunku do systemu wizyjnego (Rys. 2). Następnie, przy użyciu laserowego czujnika odległości, zintegrowanego z systemem wizyjnym, należy kontrolować, czy badany obiekt znajduje się w polu widzenia kamery.
W momencie, gdy metalowa obręcz znajdzie się w polu widzenia kamery, jest odpowiednio oświetlana przez oświetlacz pierścieniowy LED, a światło z oświetlacza rozpraszane jest przez dedykowany dyfuzor. Dzięki rozproszeniu, błyszcząca powierzchnia metalu staje się, z punktu widzenia kamery, matowa i jednolita (Rys. 3). Po ustawieniu odpowiednich parametrów akwizycji i filtracji obrazu, napis na metalowym elemencie jest prawidłowo widziany przez kamerę.
Szczegóły odnośnie kryterium wyboru poszczególnych części stanowiska są opisane poniżej.
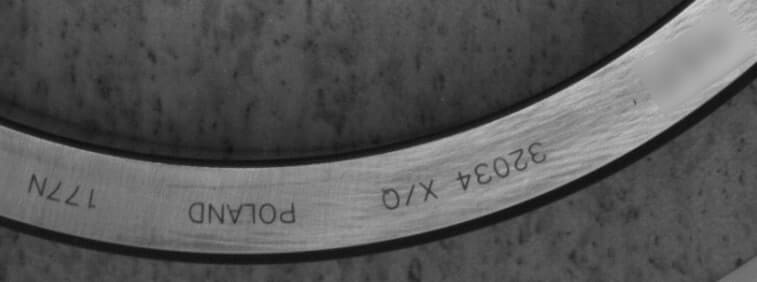
Elementy sysetmu wizyjnego
W skład systemu wizyjnego wchodzą:
- Kontroler systemu wizyjnego
- Kontroler oświetlenia
- Monochromatyczna kamera 5MPix
- Obiektyw o małej dystorsji
- Oświetlacz pierścieniowy, biały
- Dedykowany do inspekcji dyfuzor światła wykonany na zamówienie w technologii druku 3D lub innej.
Kontroler systemu wizyjnego
Kontroler został wybrany ze względu na możliwości programowe i czas przetwarzania obrazu o rozdzielczości 5MPix. Wybrany kontroler umożliwia także wyszukanie wzorców na obrazie (algorytm opisany w następnej sekcji).
Kamera i obiektyw
W proponowanym systemie wizyjnym, ze względu na typ badanego obiektu, wybrano kamerę monochromatyczną. Z uwagi na to, że element łożyska ma dużą średnicę w stosunku do badanego na nim napisu, w trosce o dobrą widoczność szczegółów i poprawną odczytanie oznaczeń na łożysku zdecydowano się użycie kamery 5M Pix.
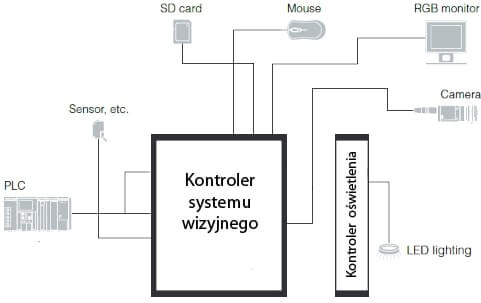
Podczas inspekcji nie jest wymagana informacja o kolorze. Rozdzielczość kamery wynosi 2432×2050 pikseli, a czas akwizycji jednej ramki wynosi 61 ms.
Obserwowany przez kamerę obszar wynoszący 300 mm (w pionie), przy rozdzielczości 2050 pix (w pionie), da nam pionową rozdzielczość systemu na poziomie 0,14 mm/pix. Mając na uwadze fakt, że oznaczenia na metalowej obręczy mają 5 mm, powyżej obliczona rozdzielczość systemu wizyjnego jest wystarczająca w celu prawidłowego wykrycia oznaczeń na powierzchni metalowej obręczy.
Podczas testów, wybrano obiektyw o odległości fokalnej równej 12 mm, umieszczony na wysokości 500 mm od podstawy badanego elementu. Zapewnił on prawidłową obserwację całego obszaru, w którym mógłby wystąpić napis. Wykres pola widzenia obiektywu w stosunku do odległości jego działania przedstawia Rys. 5.
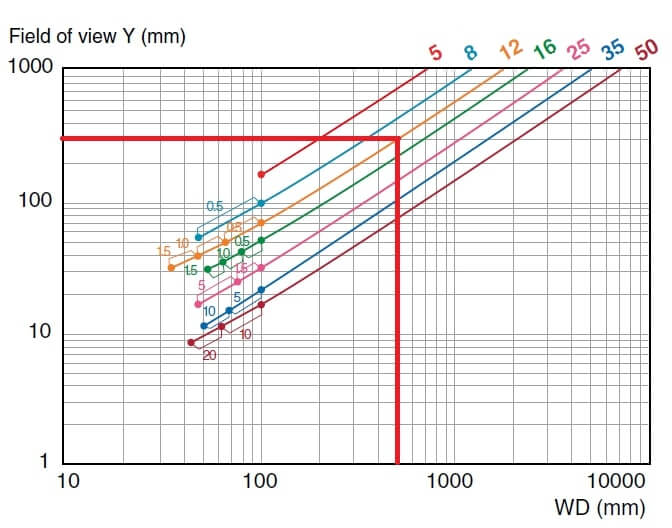
Obiektyw wybrano nie tylko na podstawie pola widzenia FoV (ang. field of view), czy ilości miejsca na montaż, tzw. WD (ang. working distance), ale również na podstawie parametru dystorsji (wynoszącym w tym przypadku jedyne 0,12%), czy liczbie cykli na mm (wynoszącym w tym przypadku aż 200 cykli/mm w środku pola widzenia, 140 cykli na mm na peryferiach pola widzenia).
Oświetlacz
Na początku do inspekcji zakładano użycie systemu „inteligentnego oświetlania”. Oświetlacz w tym systemie jest podzielony na 8 segmentów, w których każdy może świecić niezależnie od siebie. W wyniku oświetlenia obiektu od każdej strony, w wyniku połączenia wszystkich obrazów, dostajemy pseudo-mapę głębokości sceny.
Oświetlacz ten idealnie nadałby się do inspekcji wypalonych laserem znaków na metalowej powierzchni – znaki znajdowały się we wgłębieniu w stosunku do powierzchni na której się znajdowały.
Powyższy oświetlacz okazał się jednak zbyt mały do inspekcji elementu o średnicy 260 mm – największy oświetlacz w ofercie producenta ma średnicę wewnętrzną równą 200 mm.
Na podstawie wewnętrznej analizy zaproponowaliśmy własne wykonanie oświetlacza kopułkowego, który odpowiednio oświetlał błyszczącą powierzchnię metalu (Rys. 6). Oświetlacz był wykonany w technologii druku 3D. Rozproszone światło pochodzące z oświetlacza LED, zapewniło zmatowienie oraz ujednolicenie badanej powierzchni elementu łożyska i łatwą ekstrakcję cech. Widok z kamery matowego już elementu łożyska przedstawia Rys. 3.
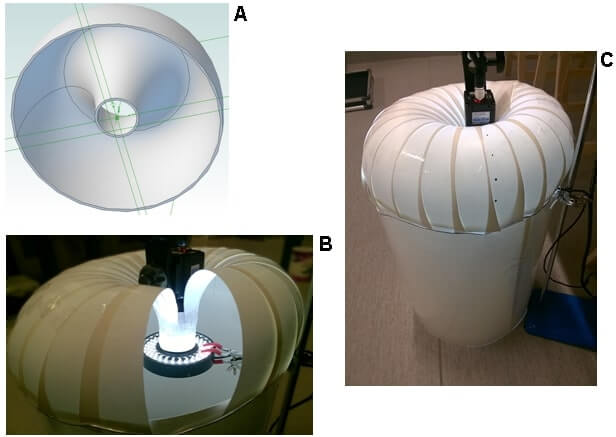
Algorytm inspekcji wizyjnej
Początkowo, jako algorytmu wyszukania zdublowanych napisów na detalu poddawanym inspekcji, firma produkująca metalowe obręcze, chciała użyć techniki OCR (ang. optical character recognition) w celu rozpoznawania znaków alfanumerycznych. W związku z powyższym, podczas wykrywania znaków, które nakładają się na siebie, istnieje wiele problemów mogących pojawić się podczas inspekcji – opisano je poniżej.
Po pierwsze, niewiele firm w swoich rozwiązaniach posiada wbudowane algorytmy umożliwiające odczytywanie „krzywych” napisów umieszczonych na łuku (w omawianym temacie, umieszczonych na metalowej obręczy). W przypadku niektórych firm konieczne było by „prostowanie” tych napisów z użyciem przekształceń geometrycznych obrazu, co wiąże się ze zwiększeniem czasochłonności obliczeń.
Po drugie, trzeba by było stworzyć tablicę wzorców znaków, które mają być wykrywane. Niestety stworzone wzorce nie odpowiadały by określonym znakom alfanumerycznym, w przypadku nakładania się znaków na siebie. Algorytm OCR nie działałby poprawnie i dawałby błędne wyniki.
Z powyższych względów, inżynierowie z CUBE SYSTEMS zaproponowali ze zrezygnowania z techniki OCR, która odczytuje pojedyncze znaki, na rzecz techniki wyszukania wzorca na obrazie, wykrywającego całe oznaczenia. Algorytm ten zadziała nawet w przypadku wzorców nakładających się na siebie. Opis algorytmu i jego etapy, znajdują się poniżej.
Etapy algorytmu automatycznej inspekcji wizyjnej:
1. Ustawienie odpowiednich parametrów akwizycji obrazu i wstępna korekcja obrazu
2. Automatyczne wykrycie znaku firmowego lub innego powtarzającego się napisu na metalowej obręczy za pomocą funkcji wyszukującej wzorzec – region wzorca przedstawiono na Rys.7.
Sekwencje znajdujące się na elementach łożysk dostarczonych do testów są następujące:
- „NAZWA_FIRMY 32034 X/Q POLAND 177N”
- „NAZWA_FIRMY 32034 X/Q POLAND 252N”.
3. Filtracja obrazu. Dodatkową filtrację obrazu należy zastosować w trudnych przypadkach inspekcji, czyli w przypadku, gdzie napisy na metalowej obręczy pokrywają się i są niemożliwe do automatycznego odczytania. Przykładem trudnej inspekcji może być wyszukanie znaku „POLAND” nałożonego na ten sam znak z małym przesunięciem, lub wykrycie znaku „POLAND” nałożonego w całości na sekwencję „32034 X/Q”. W tej sytuacji obraz wejściowy należy wzmocnić tak, aby ułatwić przeprowadzenie inspekcji i wykrycie wzorca. Zastosowanie wzmocnienia obrazu przedstawiono na rys. 8.
4. Liczba wykrytych znaków „POLAND” w obrazie będzie wpływać na końcowy wynik inspekcji wizyjnej. Tylko jednorazowe wystąpienie znaku „POLAND” będzie traktowane przez algorytm jako „OK” – inspekcja poprawna. Zero wyszukanych na obrazie znaków „POLAND” lub liczba znaków „POLAND” większa niż jeden będzie oznaczana jako „NG” – inspekcja negatywna.
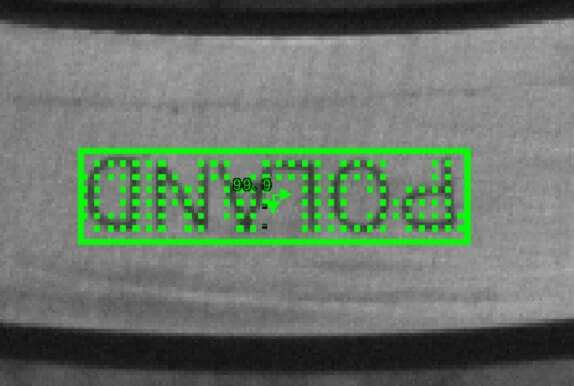
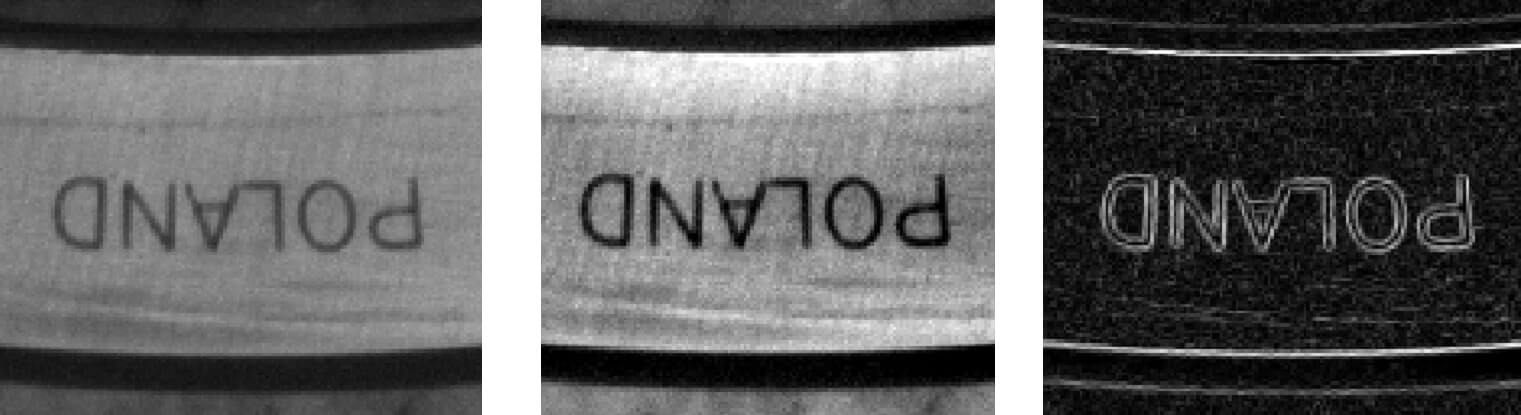
Podczas testów użyto środowiska przetwarzającego obrazu i umożliwiającego akwizycję obrazu z kamery. Środowisko pod względem programistycznym spełnia założenia szybkiego prototypowania algorytmów przetwarzających obrazy.
CUBE SYSTEMS realizuje projekty związane z integracją systemów wizyjnych. Proponowane rozwiązania dobieramy z najwyższą starannością. Przed każdą realizacją projektu, obowiązkowo sprawdzamy, czy zaproponowane rozwiązanie systemu wizyjnego spełni Twoje oczekiwania. Chcesz się dowiedzieć więcej co oferujemy? Sprawdź TUTAJ.
Udostępnij:
- #SystemyWizyjne
- #SystemyPomiarowe
- #WizjaMaszynowa
- #KontrolaJakosci
- #QA
- #PrzetwarzanieObrazu
- #WyszukiwanieWzorca
- #RozpraszanieSwiatla
- #BlyszczacaPowierzchnia